GA 700
Highlights
- One drive controlling any induction, permanent magnet or synchronous reluctance motor
- Built in EMC filter, DC choke, braking chopper reduce panel space
- Easy motor setup without the need for auto-tunning simplifies tuning with connected machinery
- Effortless Network Integration by support of all major networks with cost effective gateway feature
- Reduced set-up time wth an intuitive keypad, navigation and start-up wizards
- Keypad with automatic parameter backup function, real time clock, data logger and copy unit
- Powerful DriveWizard PC tool for drive management, start-up, programming and failure analysis
- DriveWorksEZ for programming tool for extending functionality by logic programming
- Cloud-connected DriveWizard Mobile app for drive management on smartphones and tablets
- Convenient commissioning by programming without main power from PC or Android Smart Phone
- Increased safety and reliability with built in STO SIL3 functional safety
- Side-by-side and heatsink out the back mounting for minimum panel size and optimized cooling
- Ambient temperature of 50 0C without derating (IP20), max 60 0C wth derating
- Meets Global Standards
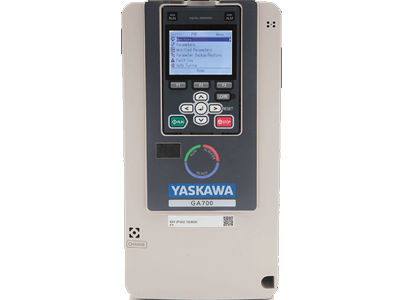
Application
High Performance type general purpose drive
3 Ph 200 V Class : 0.4 to 110kW
3 Ph 400V Class : 0.4 to 315kW
Three- Phase AC 200V
GA700 Model Number | HD | ND | ||
---|---|---|---|---|
Code | kW | A | kW | A |
CIPR-GA70D2004 | 0.4 | 3.2 | 0.75 | 3.5 |
CIPR-GA70D2006 | 0.75 | 5 | 1.1 | 6 |
CIPR-GA70D2008 | 1.1 | 6.9 | 1.5 | 8 |
CIPR-GA70D2010 | 1.5 | 8 | 2.2 | 9.6 |
CIPR-GA70D2012 | 2.2 | 11 | 3 | 12.2 |
CIPR-GA70D2018 | 3 | 14 | 3.7 | 17.5 |
CIPR-GA70D2021 | 3.7 | 17.5 | 5.5 | 21 |
CIPR-GA70D2030 | 5.5 | 25 | 7.5 | 30 |
CIPR-GA70D2042 | 7.5 | 33 | 11 | 42 |
CIPR-GA70D2056 | 11 | 47 | 15 | 56 |
CIPR-GA70D2070 | 15 | 60 | 18.5 | 70 |
CIPR-GA70D2082 | 18.5 | 75 | 22 | 82 |
CIPR-GA70D2110 | 22 | 88 | 30 | 110 |
CIPR-GA70D2138 | 30 | 115 | 37 | 138 |
CIPR-GA70D2169 | 37 | 145 | 45 | 169 |
CIPR-GA70D2211 | 45 | 180 | 55 | 211 |
CIPR-GA70D2257 | 55 | 215 | 75 | 257 |
CIPR-GA70D2313 | 75 | 283 | 90 | 313 |
CIPR-GA70D2360 | 90 | 346 | 110 | 360 |
CIPR-GA70D2415 | 110 | 415 | – | – |
Three- Phase AC 400V
GA700 Model Number | HD | ND | ||
---|---|---|---|---|
Code | kW | A | kW | A |
CIPR-GA70D4002 | 0.4 | 1.8 | 0.75 | 2 |
CIPR-GA70D4004 | 0.75 | 3.4 | 1.5 | 4 |
CIPR-GA70D4005 | 1.5 | 4.8 | 2.2 | 5 |
CIPR-GA70D4007 | 2.2 | 5.5 | 3 | 7 |
CIPR-GA70D4009 | 3 | 7.2 | 3.7 | 9 |
CIPR-GA70D4012 | 3.7 | 9.2 | 5.5 | 12 |
CIPR-GA70D4018 | 5.5 | 14.8 | 7.5 | 18 |
CIPR-GA70D4023 | 7.5 | 18 | 11 | 23 |
CIPR-GA70D4031 | 11 | 24 | 15 | 31 |
CIPR-GA70D4038 | 15 | 31 | 18.5 | 38 |
CIPR-GA70D4044 | 18.5 | 39 | 22 | 44 |
CIPR-GA70D4060 | 22 | 45 | 30 | 60 |
CIPR-GA70D4075 | 30 | 60 | 37 | 75 |
CIPR-GA70D4089 | 37 | 75 | 45 | 89 |
CIPR-GA70D4103 | 45 | 91 | 55 | 103 |
CIPR-GA70D4140 | 55 | 112 | 75 | 140 |
CIPR-GA70D4168 | 75 | 150 | 90 | 168 |
CIPR-GA70D4208 | 90 | 180 | 110 | 208 |
CIPR-GA70D4250 | 110 | 216 | 132 | 250 |
CIPR-GA70D4296 | 132 | 260 | 160 | 296 |
CIPR-GA70D4371 | 160 | 304 | 200 | 371 |
CIPR-GA70D4389 | 200 | 371 | 220 | 389 |
CIPR-GA70D4453 | 220 | 414 | 250 | 453 |
CIPR-GA70D4568 | 250 | 453 | 315 | 568 |
CIPR-GA70D4675 | 315 | 605 | 355 | 675 |
Control Characteristics | |
Product | GA700 |
Type | General Purpose AC drive with advanced vector control |
Rated Output Voltage (dependent on input) | Three Ph 200V Class : 200 to 240VAC Three Ph 400V Class : 380 to 480VAC |
Motor Types | Induction Motor, Permanent Magnet Motor (IPM/SPM), Synchronous Reluctancec Motor ( SynRM) |
Control Methods | V/f Control (V/f) V/f Control with PG ( V/f w PG) Open Loop Vector Control (OLV) Closed Loop Vector Control (CLV) Advanced Open Loop Vector Control (AOLV) OLV for PM (OLV/PM) Advanced open loop vector control for PM (AOLV/PM) CLV for PM (CLV/PM) EZ Open Loop Vector Control (EZOLV) |
Speed Control Range | 1:20 OLV/PM 1:40 for V/f, V/f w PG 1:100 for AOLV/PM, EZOLV 1:200 for OLV, AOLV, 1:1500 for CLV, CLV/PM |
Starting Torque | 150% @3Hz for V/f , V/f w PG 200% @0.3Hz for OLV, AOLV 200% @ 0rpm for CLV,AOLV/PM, CLV/PM 100% @5% speed for OLV/PM 100% @1% speed for EZOLV |
Frequency Range | 0 to 590Hz |
Braking Transistor | Built-in upto 75kW HD rating |
Frequency Accuracy | Digital reference: within ±0.01% of the max. output frequency (-10°C to +40°C) Analog reference: within ±0.1% of the max. output frequency (25°C±10°C) |
Frequency Setting Resolution | Digital reference: 0.01 Hz Analog reference: 1/2048 of the maximum output frequency setting (11 bit) |
Output Frequency Resolution |
0.001 Hz |
Torque Limit | Parameter settings allow separate limits in four quadrants in Open Loop Vector Control, Advanced Open Loop Vector Control for PM, and EZ Open Loop Vector Control. |
Accel/Decel time | 0.0 to 6000.0 seconds |
Environmental Factors | |
Ambient Temperature | -10˚C to +50˚C ( No Deration required), Upto 60˚C with deration factor |
Altitude | 1000 m or less with no deration . Altitudes over 1000 m and up to 4000 m are possible by derating the output current by 1% for every 100 m. |
Humidity | 95% RH or less (no condensation) |
Surrounding Area | Pollution degree 2 or less |
Shock | ・ 10 Hz to 20 Hz, 1 G (9.8 m/s2) ・ 20 Hz to 55 Hz, 0.6 G (5.9 m/s2) |
Area of Use | Indoors |
Protection Features | |
Motor Protection | Motor overheat protection based on output current |
Momentary Overcurrent Protection |
Drive stops when output current exceeds 200% of the HD output current. |
Overload Protection | Drive stops when the output current exceeds these overload tolerances. ・ HD Rating: 150% of the drive rated output current for 60 s. ・ ND Rating: 110% of the drive rated output current for 60 s. |
Overvoltage Protection | 200 V class: Stops when the DC bus voltage is more than approximately 410 V 400 V class: Stops when the DC bus voltage is more than approximately 820 V |
Undervoltage Protection | 200 V class: Stops when the DC bus voltage decreases to less than approximately 190 V 400 V class: Stops when the DC bus voltage decreases to less than approximately 380 V |
Momentary Power Loss Ride-Thru |
Stops when power loss is longer than 15 ms. Continues operation if power loss is shorter than 2 s (depending on parameter settings). |
Heatsink Overheat Protection |
Thermistor |
Stall Prevention | Stall prevention during acceleration/deceleration and constant speed operation |
Ground Fault Protection | Protection by electronic circuit |
Charge LED | Charge LED illuminates when DC bus voltage is more than 50 V. |
Standards Compliance | ・UL61800-5-1 ・Two Safe Disable inputs and 1EDM output according to ISO/EN13849-1 Cat.3 Ple,IEC/EN61508 SIL3 ・EN61800-3:2004+A1:2012 ・IEC/EN61800-5-1 |
Power Specifications | |
Rated input Voltage/Frequency | 400V Class: ・Three-phase AC power supply 380 V to 480 V 50/60 Hz ・DC power supply 513 V to 679 V 200V Class : ・Three-phase AC power supply 200 V to 240 V 50/60 Hz ・DC power supply 270 V to 340 V |
Allowable Voltage Fluctuation |
−15% to 10% |
Allowable Frequency Fluctuation |
±5% |
Common Specifications | |
Carrier Frequency | Derating the output current enables a maximum of 15 kHz to be set.( Based on rating ) |
Multi Function Digital Inputs | 8 Digital Inputs ( NPN or PNP ) , 24VDC. External and internal power source possible |
Multi Function Digital Outputs | 3 Programmable Relay M1-M2, M3-M4, M5-M6 (AC 250 V, max. 1 A DC 30 V, max. 1 A min. load DC 5 V, 10 mA) and 1 fault relay MA-MB-MC |
Multi Function Analog Inputs | 3 Multi function Analog input A1, A2 & A3 ( -10 to +10 Vdc (20 kΩ)/ 0 to 10 Vdc (20 kΩ) 0 to 20 mA (250 Ω)/ 4 to 20 mA (250 Ω) |
Multi Function Analog Output | 2 Multi function Analog outputs FM-AC & AM-AC (0 – 10 V/4 – 20 mA (250 Ω)) |
Pulse Train | 1 Pusle Train output (0 – 32 kHz (2 kΩ)) 1 Pulse Train input (max 32mA) |
Serial communication | MEMOBUS/Modbus (RTU mode) comm. RS-485, Max. 115.2 kbps |
DC Supply | DC 24 V Power supply, Output 24 V, max. 150 mA |
Optional communication Protocols | Mechatrolink, Profibus, Profinet, Ethernet TCP/IP, Modbus TCP/IP, CC-Link, Canopen, Bacnet, Devicenet, EtherCAT, Lonworks |
Programming Interface | Serial port or Mini-USB in front of VFD |
Additional Functions | Torque Control, Droop Control, Speed/Torque Control switch, Feed Forward Control, Zero Servo Control, Momentary Power Loss Ride-Thru, Speed Search, Overtorque detection, torque limit, 17 Step Speed (max.), accel/decel switch, S-curve accel/decel, 3-wire sequence, Auto-Tuning (rotational, stationary), Dwell, cooling fan on/off switch, slip compensation, torque compensation, Frequency Jump, Upper/lower limits for frequency reference, DC Injection Braking at start and stop, Overexcitation Deceleration, High Slip Braking, PID control (with Sleep function), Energy Saving Control, MEMOBUS/Modbus (RTU mode) Communications (RS-485, max. 115.2 kbps), Fault Restart, Application Presets, DriveWorksEZ (customized functions), Parameter Backup Function, Online Tuning, KEB, Overexcitation Deceleration, Inertia Tuning and ASR Tuning, Overvoltage Suppression, High Frequency Injection, etc. |
Highlights
- The software can be used to control both Induction and Permanent Magnet Motors.
- NO physical anti-vibration design like thick, high-strength pipes and reinforcements for the installation sections are required.
- Low Audible Noise.
- Life Extension and Long Service Life.
- An all in one equipment that not only controls the compressor but also the Vibration in the machine.
- Reduces Drive reinforcement costs and machine failure rates due to vibration
Download
Catalogue
High Performance type general purpose drive
GA700 Ratings:
- 3 Ph 200 V Class : 0.4 to 110kW
- 3 Ph 400V Class : 0.4 to 315kW
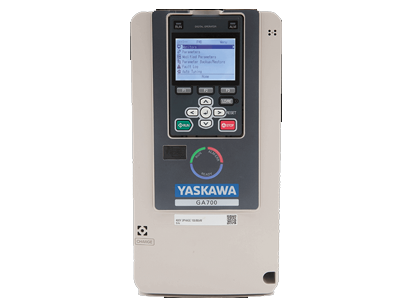
YASKAWA has got profound experience in the Material handling industry derived from long term partnerships with OEM’s and End customers. Application specific solutions ensure high efficiency and profitability for its customers.
FEATURE 1: ADVANCED MECHANICAL BRAKE CONTROL
- Intelligent in-built brake control function ensures smooth opening and closing of mechanical brakes.
- Reduces wear and tear of brake shoes in turn increase its lifespan.
- Prevents slippage of load & ensures complete security.
- Dedicated crane parameters reduce the installation time.
- Individual torque control in all 4 quadrants of operation.
FEATURE 2: ROPE SLACK PREVENTION
- Avoids slackness of rope while placing the load
- Maintain tightness by rotating the drum in opposite direction
- Saves operating time
- Maintains Tensile strength of the rope
- Increases productivity
FEATURE 3: IMPACT STOP
- Drive senses any impact on the load and runs in lower speed for some time
- If the Run command is also removed, the drive will stop after monitoring torque reference
- Enhances safety
FEATURE 4: ZERO SPEED REGULATION
- Protection against mechanical brake failures during NO RUN command
- DC injection function provides required torque to hold the load
- Alarms the operator about mechanical brake failure.
- Enhances safety
FEATURE 5: SWIFT LIFT FUNCTION
- This function saves operating time of hoist during No- Load condition
- In built intelligent function provides dynamic speed control by load detection
- No external load sensor required
- Reduces cycle time
- Improves operational efficiency
- Increases productivity
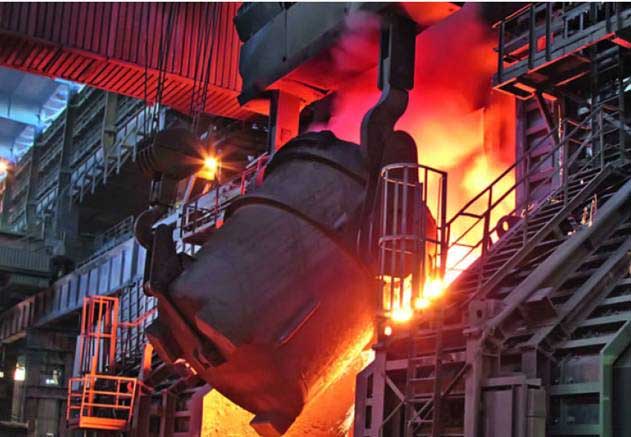
FEATURE 6: TRAVEL LIMIT
- Prevent the load from travelling beyond a predefined point.
- Reduces physical damages due to uncontrolled operations.
- Multi-function digital inputs can be configured for forward or reverse travel limits.
- Provides the safety operation for the Long / cross travel.
FEATURE 7: COMPACT FOR BUILDING INTO MACHINE
- Smaller footprint drives ensure high compatibility.
- Panel provision in single girder cranes can be eliminated.
FEATURE 8: IMPROVED LOAD CONTROL
- Dedicated acceleration and deceleration parameters for smooth operation.
- Prevents shocks and load swings.
- Allows very accurate load positioning
FEATURE 9: HIGH AMBIENT TEMPERATURE OPERATION
- YASKAWA Drives are designed to operate upto 60ºC.
- Deration of the drive current above 50ºC.
- Drives are designed to operate in Humidity / Dust operation
FEATURE 10: MULTI SPEED REFERENCE
- Controls the crane on multi speeds, allowing customer to customize as per the requirement.
- Multiple speed references (17 speeds) are available.
- Provides smooth operation of crane and prevent jerk.
FEATURE 11: SAFE TORQUE OFF
- Provides a redundant hardware safety circuit
- Isolates the Drive and Motor during an Emergency with safe torque off function.
- Eliminates the need for external circuit for isolating the power.
- It allows easy maintenance of the motor / mechanical system without Drive power off.
FEATURE 12: SLIP COMPENSATION
- It ensures the speed regulation and accuracy in both hoisting directions.
- Reduces operating time.
- Improves speed response
FEATURE 13: MOTOR PHASE LOSS DETECTION
- Causes the drive to fault and commands the brake to set if an input or output phase loss occurs.
- Prevents over heating of motor due to output phase loss.
FEATURE 14: ADVANCED TORQUE CONTROL
- Ensures the full load torque at zero RPM
- Monitor over load & load loss and perform load sharing operation for multiple hoist cranes.
- Detects over torque and under torque condition
Crane Software Drive – GA 700
Ratings:
- 3 Ph 400V Class : 0.4 to 315kW
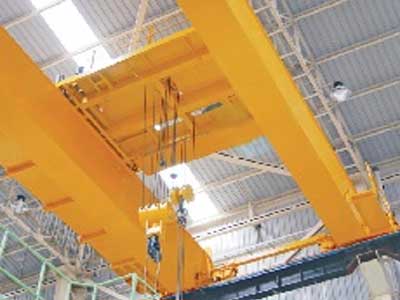